External soft start
DC-DC buck converters all have a soft-start function. After the converter starts up, the duty cycle increases gradually, allowing the output voltage to rise smoothly, which avoids inrush currents due to sudden charging of the output capacitors. Converters with internal soft start will have a constant soft start time. If the application requires a very large output capacitor or a specific soft-start time, it is better to choose a converter with an externally controlled soft-start, where the soft-start time can be set by the external capacitor.
External compensation
The error amplifier of a current-mode converter needs to be compensated to ensure the stability of the circuit. Type II compensation elements determine the bandwidth and phase of the DC converter. Externally compensated converters are more flexible in setting the required bandwidth and phase margins even with different types of output capacitors and a wide range of input and output voltages.
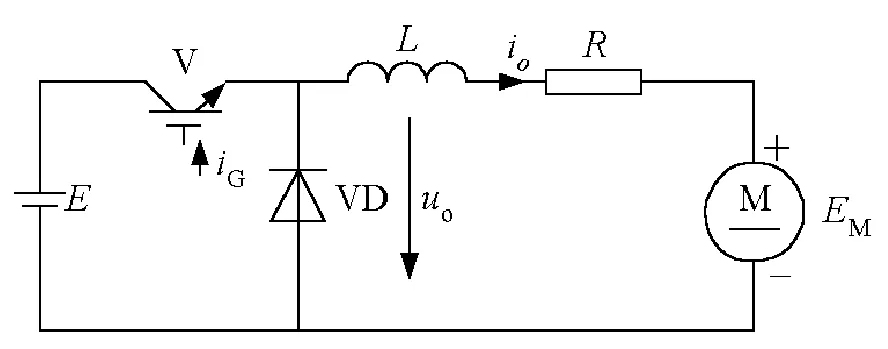
Settable frequency
Some converters have a set frequency feature: that is, the switching frequency can be set by an external resistor, providing the flexibility to choose the best switching frequency. Choosing a higher frequency reduces ripple, device size, and provides better transient performance. Choosing a lower frequency can improve efficiency or reduce higher order harmonics.
External synchronization input
Some current-mode converters have external synchronization inputs to synchronize the internal clock with the external clock signal, which allows precise setting of the switching frequency (in more sensitive frequency bands, noise can be avoided) and also allows multiple converters to operate at the same frequency simultaneously.
Low differential pressure mode or 100% duty cycle mode
Many series of current-mode DC-DC buck converters feature a low dropout mode: these buck converters slowly increase the duty cycle as the input drops, and continuously turn on the high-side MOSFET when the input voltage falls below the regulated target voltage. this feature is particularly suitable for battery-powered applications; it extends battery life when the battery power is almost depleted.
The function of Power Good is to monitor the output signal of the Buck converter and to inform the system that the output voltage is in a specific operating range. Power Good can be used for system initialization, fault protection, or start-up procedures.
Over Current Protection: All buck converters have Over Current Protection. When the inductor current exceeds the value, the duty cycle of the converter is limited. If the load continues to increase, it will cause the output to sink. However, when overload occurs, the system will handle it in several different ways.
Lockout Mode OCP: When an overload occurs and the output voltage falls below the under voltage protection value, the system will shut down and lockout. The converter needs to be re-enabled or re-powered to restart. This method ensures zero power consumption after an overload, but does not automatically restart.
Hiccup mode OCP: When an overload occurs and the output voltage falls below the under voltage protection value, the system shuts down and restarts with a soft start. A sustained overload will see the shutdown/restart cycle occur continuously, also known as hiccup mode. The advantage of hiccup mode is the low average overload current and the automatic restart when the overload condition disappears.
No Undervoltage Protection: When an overload occurs, the output voltage is reduced, but there is no undervoltage protection (UVP). During the overload period, the system continues to operate at OCP current. When the overload condition disappears, the output voltage is immediately restored. However, continuous operation at OCP current can cause an increase in temperature during a long-term overload condition.